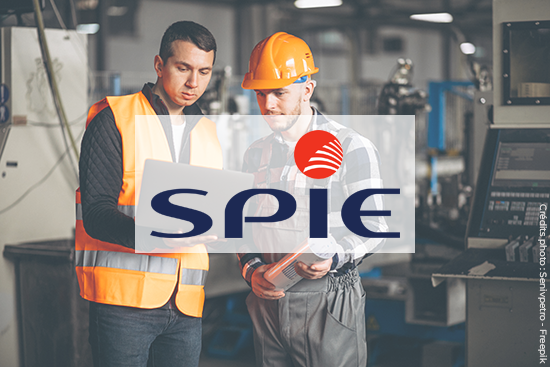
About SPIE
SPIE provides a wide range of services in climate engineering, thermal engineering, communications, electrical installations and energy. The DML Department, “Deployment, Maintenance and Logistics”, of the Île-de-France/Nord-Ouest subsidiary offers multi-technical maintenance and repair services for large companies with branch networks (banks, telecommunications, service companies, energy supply) and desires centralized management for the whole territory.
Within this framework, SPIE is also involved in the maintenance of thermal equipment, the repair of small electrical equipment or the implementation of a national plan to change brands for a network of 10,000 points of sale.
Key figures
The SPIE Group
- 46,500 employees;
- 6.7 billion euros revenue in 2018;
- 4 activities: Information & Communication Technologies, Mechanical & Electrical, Technical Facility Management, Transmission & Distribution.
The DML department
- 200 technicians;
- 4 to 6 interventions per day and per technician;
- 7 Million kilometers per year.
The challenge
Until a few years ago, the planning was done manually by 6 logisticians each organizing the work of a group of technicians without necessarily communicating with each other. The adoption of a geolocation system has revealed that technicians spent a huge time on the road. “This justified the search for a centralized tool that would allow a better allocation of interventions to technicians and help reduce even 10% of the 7 million kilometres travelled each year” says Mr. Cyril Duval.
La solution apportée par GEOCONCEPT
The choice of SPIE focused on Opti-Time, in particular for its ability to plan in real-time and the user-friendliness of its interface. Indeed, the technicians are permanently in the field and the system should be able to integrate new priority requests at any time and transmit them to the mobile teams' devices.
The planning takes into account many parameters: agency opening hours, technicians' skills, proximity to the home for the start of tours, contractual obligations, etc. In case of urgent corrective action, the system looks at whether there is a planned preventive task within the next 30 days and within a 3 km radius, which can then be “sucked up” and done in the process.
Technicians start their day with the knowledge of their first 2 interventions. The following ones arrive in a “drop by drop” mode according to the evolution of the schedule.
Résultats
Automatic transmission of 80% of service requests
Faster report entry
Guaranteed traceability
"The solution ensures a much better consistency of the schedules and avoids any conflict of attribution, the technician being chosen by the system. Opti-Time also allows us to know the kilometers covered, which can prove to be a competitive advantage: customers who outsource the maintenance of their agencies are more and more attentive to this information, particularly with a view to reducing their greenhouse gas emissions."
The ergonomics of Opti-Time have facilitated its adoption by logisticians. Their number of calls decreased because 80% of the requests for interventions are automatically planned and sent. The solution guarantees traceability throughout the activity thanks to the mobile portal: the technicians can type the status of the intervention and can enter a quick report. Today the solution organizes the schedule of 40 technicians: it will be deployed on around 80 very quickly and gradually on the 200 technicians of the Deployment, Maintenance and Logistics Department.